How long does it take to drill a water well? It’s a question with no single answer, hinging on a whole load of factors. From the rock type to the rig’s power, the well’s depth, and even the water quality, every element plays a part in the total drill time. It’s a bit like trying to work out how long it takes to build a house – it depends on so many things.
Some digs are a breeze, while others can be a right nightmare. Get ready to dive into the murky depths of well-drilling, where time is money, and even the smallest details can mean a huge difference.
The drilling process, from the initial site assessment to the final water test, can be a complex and time-consuming operation. Different methods, like rotary drilling or cable tool drilling, have their own unique pros and cons when it comes to speed. Understanding these factors will give you a much clearer picture of the total drill time.
Factors Affecting Drilling Time
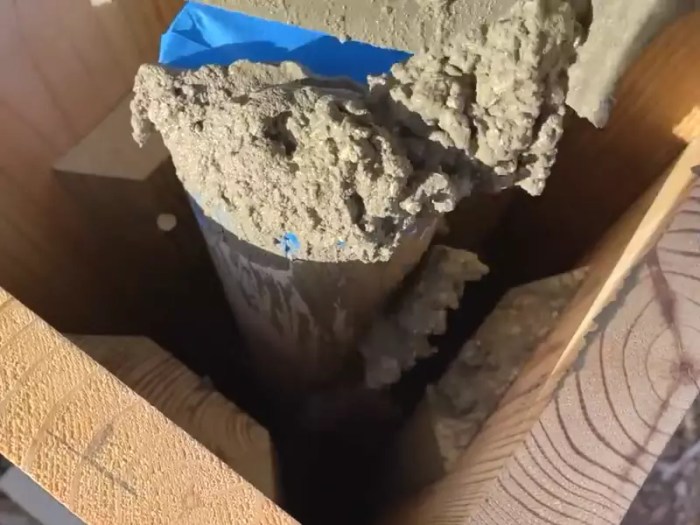
Water well drilling, a crucial process for accessing groundwater, is a complex operation influenced by a multitude of factors. Understanding these factors is vital for project planning and accurate cost estimation. From the geological formations encountered to the specifications of the drilling rig, each element plays a critical role in determining the overall time required for the well’s completion.Drilling time is not a fixed parameter but a dynamic value, varying significantly depending on the conditions encountered during the process.
These conditions often require adjustments to drilling strategies and techniques, thus impacting the overall timeline.
Geological Formation Influence
Geological formations significantly influence drilling time. Different rock types possess varying degrees of hardness and density, directly affecting the drilling speed. The depth of the water table also plays a pivotal role. Deeper water tables require more time to reach the aquifer. Moreover, the presence of fractured zones, cavities, or other geological anomalies can dramatically impact drilling efficiency and, consequently, the duration of the operation.
- Rock Types: Harder rock types, such as granite and basalt, necessitate more powerful drilling equipment and specialized drill bits, resulting in extended drilling times. Conversely, softer rock types, like sandstone and shale, are generally drilled more quickly.
- Hardness: The hardness of the rock directly correlates with the rate at which the drill bit can penetrate. Harder rocks require more energy to cut, leading to slower progress.
- Water Table Depth: The depth of the water table is a crucial factor. Reaching deeper water tables typically necessitates more drilling time, as the drill must penetrate deeper strata.
- Geological Anomalies: The presence of unexpected geological features, such as fractures or cavities, can create complications and potentially necessitate adjustments to the drilling plan, thus extending the drilling time.
Drilling Rig Specifications
The specifications of the drilling rig significantly affect the drilling process duration. Rig horsepower, the type of drill bit employed, and the overall efficiency of the equipment directly influence the drilling rate. A more powerful rig with an appropriately designed drill bit for the specific rock type can substantially reduce drilling time.
- Horsepower: A rig with greater horsepower is capable of drilling through harder formations more efficiently, thus reducing the overall drilling time. A less powerful rig may require more time for the same task.
- Drill Bit Type: The type of drill bit directly impacts drilling efficiency. Specific drill bits are designed for different rock types, and choosing the correct bit is crucial for maximizing drilling speed. Using an inappropriate drill bit for the given geological formation can result in slower progress and prolonged drilling time.
- Rig Maintenance: Regular maintenance and efficient operation of the drilling rig are critical factors. Proper maintenance ensures optimal performance, whereas equipment malfunction can cause delays and extend the drilling time significantly.
Terrain Influence
The terrain in which the drilling operation takes place can significantly influence the duration of the process. Drilling in soft soil requires different techniques and equipment than drilling in hard rock formations. In soft soil, the risk of the well collapsing is higher, requiring extra measures to ensure stability and safety, which may extend the drilling time.
- Soft Soil: Drilling in soft soil often involves specialized drilling techniques and potentially more time-consuming procedures to maintain the wellbore’s stability. The presence of loose sediments or water-saturated soil can significantly hinder drilling speed.
- Hard Rock: Drilling in hard rock requires more powerful equipment and specialized drill bits. The process may take longer due to the resistance offered by the rock formations.
Typical Drilling Times
The following table provides estimated drilling times for different rock types, but these are just general guidelines. Actual drilling time will vary based on specific geological conditions, rig specifications, and other factors.
Rock Type | Estimated Drilling Time (hours/ft) | Description | Image Description |
---|---|---|---|
Sandstone | 0.5-1.0 | A sedimentary rock composed primarily of sand-sized minerals, often relatively soft and easy to drill. | A close-up view of a sandstone sample with visible grain structure. |
Granite | 1.5-3.0 | An igneous rock with a crystalline structure, known for its hardness and resistance to drilling. | A rock face with visible granite crystals and texture. |
Shale | 0.8-1.5 | A sedimentary rock composed of clay minerals, typically relatively soft and prone to sloughing. | A section of shale showing layering and potential fracturing. |
Basalt | 2.0-4.0 | A dark-colored igneous rock with a high density and hardness, requiring significant drilling power. | A fractured basalt rock face with visible columnar structure. |
Drilling Methods and Their Impact on Time
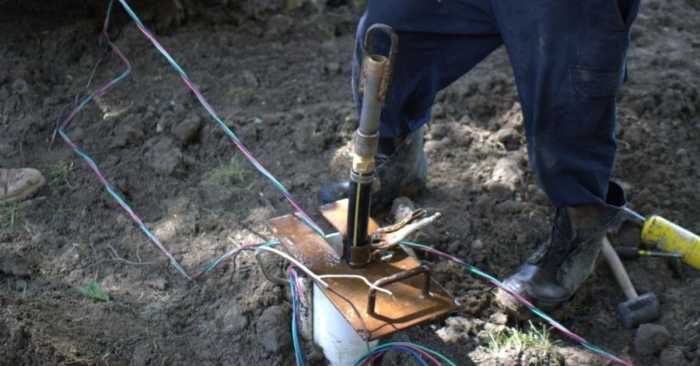
Different water well drilling methods offer varying levels of efficiency and suitability for different geological conditions. Understanding these methods and their respective impacts on drilling time is crucial for accurate project planning and cost estimation. Factors like terrain, rock type, and desired well depth significantly influence the chosen approach.
Rotary Drilling
Rotary drilling is a widely used method, especially for deeper wells and challenging geological formations. A drilling rig rotates a drill bit at high speed, cutting through the earth. The cuttings are then removed by a circulating fluid, typically a mixture of water and additives. This continuous action allows for consistent progress, especially when dealing with hard or abrasive rock formations.Rotary drilling involves a specialized rig that continuously rotates a drill bit while simultaneously circulating a drilling fluid.
The drilling fluid, often a mixture of water and chemicals, helps cool the bit, lubricate the borehole, and remove cuttings from the well. The process is controlled by a sophisticated system of pumps, motors, and valves. The speed of rotation and the pressure of the circulating fluid are key factors affecting the drilling speed. High-pressure drilling fluids are used for harder rock formations, increasing the drilling time in proportion to the hardness of the rock.
Cable Tool Drilling
Cable tool drilling is a more traditional method, often used for shallower wells and less challenging geological conditions. A heavy hammer, suspended from a cable, strikes the drill bit, breaking up the rock. The broken rock is then removed manually or with a bailer. This method is significantly slower than rotary drilling.This method, while often slower than rotary drilling, is more cost-effective for simpler geological formations and shallower depths.
The equipment is relatively less complex, leading to lower upfront costs. The hammer and cable system can be less susceptible to damage from extreme pressures or abrasive materials. However, its speed is a major drawback, often resulting in extended drilling times compared to rotary drilling.
Comparison of Drilling Methods
Drilling Method | Description | Average Drilling Time | Suitable Conditions |
---|---|---|---|
Rotary Drilling | A drilling rig rotates a drill bit, circulating fluid to remove cuttings. | Generally faster, ranging from several days to weeks depending on depth and rock type. | Hard rock formations, deeper wells, challenging geological conditions. |
Cable Tool Drilling | A hammer strikes the drill bit to break up rock; cuttings are removed manually or with a bailer. | Significantly slower, ranging from several weeks to months depending on depth and rock type. | Shallower wells, less challenging geological conditions, where cost is a major factor. |
Factors Affecting Drilling Time (Revisited)
Drilling time is highly dependent on a variety of interacting factors.
While drilling methods are a crucial factor, the complexity of the geological strata also plays a significant role. The presence of hard rock layers, fractures, or cavities can dramatically increase drilling time for both methods. The specific drilling parameters, including rotation speed and fluid pressure, need careful consideration to optimize the process and minimize time. The experience and expertise of the drilling crew also significantly impact the efficiency and speed of the process.
The availability of necessary equipment and supplies, including fuel, water, and spare parts, is critical for maintaining a consistent drilling operation.
Well Depth and its Correlation to Time: How Long Does It Take To Drill A Water Well
Drilling a water well is a process that takes time, and the depth of the well is a major factor in determining the total duration. The deeper the well, the more challenging the drilling process becomes, requiring more time and potentially more resources. This section examines the intricate relationship between well depth and drilling time, providing examples and estimations to illustrate this correlation.The relationship between well depth and drilling time is a direct one.
Generally, the deeper the well, the longer the drilling process takes. This is due to the increasing distance the drill bit needs to travel through various geological formations, each with its own characteristics in terms of hardness and resistance to penetration. This also includes the time required to manage the drilling process and maintain the equipment, which are affected by depth.
Factors Influencing Time per Foot
Drilling time per foot isn’t a constant; it varies significantly based on the specific conditions encountered during drilling. The hardness and composition of the rock strata encountered play a crucial role, as some formations require more time to penetrate than others. For instance, dense rock formations will necessitate more effort and time to penetrate compared to softer soil layers.
Similarly, the presence of obstructions or unexpected geological features can substantially increase drilling time per foot.
Typical Drilling Time per Depth
Estimating drilling time per foot is challenging, as conditions vary widely. However, some general guidelines can be provided. Drilling time per foot can be highly variable based on numerous factors, such as the specific geology of the drilling site, the type of drilling rig being used, and the operator’s experience and efficiency. For example, a well that encounters numerous hard rock layers will take longer to drill than one that primarily encounters softer sediment.
Similarly, more advanced drilling rigs can potentially penetrate the same depth in less time than older, less efficient models.
Potential Complications in Deeper Wells
Deeper wells introduce various complications that can significantly impact drilling time. These include increased wear and tear on the drilling equipment, higher risks of equipment failure, and more complex logistics in managing the drilling process. The increased depth also leads to more challenging logistics in transporting and storing materials, along with more complex maintenance procedures and potential for equipment breakdowns due to the increased strain on the drilling rig.
Moreover, the increased depth often necessitates specialized equipment and expertise to handle the challenges presented.
Correlation Table, How long does it take to drill a water well
Well Depth (ft) | Estimated Drilling Time (days) | Potential Issues |
---|---|---|
50 | 2-5 | Potential for encountering localized hardpan; minor equipment issues |
150 | 10-25 | Increased risk of equipment failure; potential for encountering substantial rock formations; logistical challenges |
300 | 30-60 | High risk of equipment failure; significant logistical challenges; need for specialized equipment and expertise; possibility of encountering complex geological formations |
500 | 60-120+ | Extreme risk of equipment failure; substantial logistical challenges; very high probability of encountering complex geological formations; specialized equipment and expertise are essential. |
Water Quality and Drilling Time
Water quality plays a crucial role in the efficiency and duration of water well drilling. The characteristics of the water encountered during drilling can significantly impact the drilling process, from the initial stages to the final completion. Understanding these factors allows for proactive planning and resource allocation, ultimately leading to more efficient and cost-effective well construction.The nature of the water encountered during drilling, including its hardness, salinity, and other constituents, can directly influence the drilling tools and techniques employed.
This can affect the rate of penetration, the wear and tear on equipment, and the overall time required to reach the desired depth and achieve a stable wellbore. Proper monitoring of water quality throughout the drilling process is vital for identifying potential issues and adapting drilling strategies to ensure successful well completion.
Influence of Water Quality on Drilling Process
Different water qualities can present varying challenges during drilling operations. High levels of hardness, for instance, can increase the friction between the drill bit and the formation, potentially leading to slower penetration rates. Similarly, high salinity levels can cause corrosion of drilling equipment, which can necessitate more frequent maintenance and replacement of parts, thereby increasing the overall drilling time.
Furthermore, the presence of suspended solids or other particulate matter in the water can clog drilling equipment, requiring additional cleaning and maintenance.
Monitoring Water Quality During Drilling
Rigorous monitoring of water quality throughout the drilling process is essential for proactive problem-solving. Regular sampling and analysis of the water encountered at different depths provide crucial insights into the formation characteristics and potential challenges. These analyses can help determine the suitability of the formation for drilling and allow for the adjustment of drilling parameters to optimize efficiency.
Various methods, including visual observation, chemical analysis, and physical testing, can be employed to determine parameters like salinity, hardness, and pH.
Common Water Quality Issues and Their Impact
Several common water quality issues can significantly affect drilling time. One prominent issue is the presence of high water tables, which can lead to increased hydrostatic pressure. This increased pressure can make drilling more difficult, potentially requiring adjustments to the drilling parameters and the use of specialized equipment. Another significant concern is the presence of abrasive materials or excessive clay content, which can lead to rapid wear on the drill bit and increase the frequency of maintenance, thus extending the drilling time.
- High Water Table: A high water table can impede drilling progress by creating hydrostatic pressure. This pressure can increase drilling difficulty, leading to slower penetration rates and potentially requiring more frequent adjustments to drilling parameters. Special techniques and equipment might be needed to mitigate the impact of high water tables, such as using heavier mud weights or more advanced drilling strategies.
- High Salinity: High salinity levels can lead to corrosion of drilling equipment, necessitating more frequent maintenance and potentially requiring the use of corrosion-resistant materials. This directly translates to increased downtime for repairs and replacements, thereby extending drilling time.
- High Hardness: High hardness levels can significantly increase friction between the drill bit and the formation. This increased friction results in slower penetration rates, demanding adjustments to the drilling parameters and potentially requiring more frequent bit changes.
- Abrasive Materials: The presence of abrasive materials in the formation water can lead to rapid wear and tear on the drill bit. This necessitates frequent bit changes, resulting in increased drilling time.
Potential Impact of Water Quality on Drilling Time
Water Quality Issue | Impact on Drilling Time | Mitigation Strategies |
---|---|---|
High water table | Increased drilling time due to higher hydrostatic pressure, requiring adjustments to drilling parameters, specialized equipment, and potentially more frequent rig trips. | Using heavier mud weights, implementing more advanced drilling strategies (e.g., directional drilling techniques), or employing wellbore stability enhancement measures. |
High salinity | Increased drilling time due to corrosion of drilling equipment, necessitating frequent maintenance and replacement of parts. | Using corrosion-resistant materials for drilling tools, implementing specialized corrosion inhibitors in the drilling fluid, and utilizing advanced corrosion monitoring techniques. |
High hardness | Increased drilling time due to increased friction between the drill bit and the formation, leading to slower penetration rates and requiring more frequent bit changes. | Using different drill bit materials, adjusting drilling parameters to optimize bit performance, or using specialized drilling fluids to reduce friction. |
Abrasive materials | Increased drilling time due to rapid wear on the drill bit, necessitating frequent bit changes. | Using drill bits with enhanced wear resistance, employing drilling fluids with improved lubricity and stability, or modifying drilling parameters to mitigate the impact of abrasive materials. |
Site Conditions and Drilling Time
Site conditions are arguably the single most influential factor in determining the overall drilling time. From the initial assessment to the final well completion, the terrain, access, and geological characteristics of the drilling site play a crucial role in the efficiency and safety of the entire process. Understanding these factors allows for better planning and resource allocation, ultimately impacting the cost and timeline of the project.Site conditions exert a significant influence on the drilling process.
They dictate the equipment needed, the procedures followed, and the overall time required for completion. Varied terrain, for example, may necessitate specialized equipment or even temporary road construction, which can dramatically increase the duration of the project. These are just some of the considerations that highlight the importance of a thorough site assessment before initiating any drilling operations.
Factors Affecting Drilling Time Due to Site Conditions
Site assessments are paramount to accurately predicting drilling time. The characteristics of the land itself significantly influence the speed and ease of drilling. Numerous factors must be considered during this assessment.
- Terrain: Uneven terrain, steep slopes, or rocky outcrops can hinder the movement of drilling equipment, necessitate specialized rigs, and increase the risk of accidents. This, in turn, directly translates to longer drilling times. For example, a site with dense vegetation or difficult terrain might require significant clearing and site preparation, extending the overall timeline.
- Access: The accessibility of the site significantly impacts drilling time. Difficult access roads, limited space, or the need for temporary infrastructure can delay the arrival of equipment and personnel, impacting the drilling schedule. Imagine a site requiring a new road to be built; this clearly adds to the project’s overall duration.
- Water Availability and Quality: Water availability is critical for drilling operations. Sufficient water supply is essential for mud mixing, cooling equipment, and various other tasks. Inadequate water sources or poor water quality can significantly delay drilling. This could lead to additional time required to find suitable water sources or to implement water treatment solutions.
- Soil Conditions: The type of soil encountered during drilling can drastically affect drilling time. Hardpan, rock formations, or highly unstable soils require different drilling techniques and equipment, leading to longer drilling times compared to softer, more readily drilled formations. For instance, encountering unexpected rock formations may necessitate the use of specialized rock bits, extending the drilling process.
- Environmental Factors: Environmental factors like weather conditions (extreme heat, rain, snow), proximity to sensitive ecosystems, or the presence of underground utilities can influence the drilling schedule. These factors must be considered to ensure the safety of personnel and the environment.
Procedures for Assessing Site Conditions and Estimating Drilling Time
Accurate assessment of site conditions is crucial for accurate time estimation. A comprehensive approach is needed.
- Detailed Site Surveys: Conducting thorough topographic surveys, geological investigations, and assessments of the surrounding environment is paramount. This involves using appropriate surveying equipment and employing qualified personnel. This detailed analysis helps anticipate potential challenges and develop strategies to mitigate their impact.
- Geological Studies: Understanding the subsurface geology is vital for predicting the type of formations encountered during drilling. This involves analyzing geological maps, conducting test borings, and employing specialized geological equipment. This step allows for accurate estimation of the anticipated drilling time.
- Access Route Analysis: Evaluate the accessibility of the site, including road conditions, potential obstacles, and necessary infrastructure improvements. Assessing the access routes allows for the development of realistic timeframes for equipment and personnel transport.
- Environmental Impact Assessments: Conduct environmental impact assessments to identify any potential environmental risks and develop mitigation strategies. These assessments ensure the drilling process complies with environmental regulations and minimizes any negative impact on the surrounding environment.
Importance of Site Preparation for Drilling Time
Adequate site preparation significantly influences the overall drilling time.
- Clearing and Excavation: Proper clearing and excavation of the drilling site can minimize delays during equipment deployment and facilitate smooth drilling operations. Clearing and excavation contribute significantly to a shorter drilling time. This is directly related to efficiency and safety.
- Infrastructure Development: Establishing necessary infrastructure, such as temporary roads, water supply lines, and power sources, minimizes potential disruptions and keeps the drilling process on schedule. Proper infrastructure development is key to a streamlined drilling operation.
- Safety Measures: Implementing safety measures and protocols on the site minimizes risks and potential delays. Proper safety procedures are critical for both worker well-being and adherence to regulatory standards.
Conclusive Thoughts
So, there you have it – a glimpse into the world of water well drilling and the factors that influence its duration. It’s clear that drilling time isn’t a fixed number, but rather a dynamic calculation based on various conditions. From the geological make-up to the rig’s capabilities, the well’s depth, and the water quality, each plays a crucial role.
By understanding these interconnected factors, you can better anticipate the time commitment involved in a water well project.
General Inquiries
What’s the average drilling time per foot?
There’s no average. It varies wildly depending on the rock type, the rig’s specs, and the well’s depth.
How does the water table affect drilling time?
A high water table can slow things down significantly, sometimes requiring special techniques and more time.
What’s the difference between rotary and cable tool drilling?
Rotary drilling is generally faster for hard rock, while cable tool drilling might be better suited for softer formations. Rotary drilling is generally the preferred method for deeper wells.
Can you provide a table of drilling times for different well depths?
Unfortunately, a general table isn’t possible due to the variable factors involved. Consult with a drilling professional for accurate estimations based on your specific site conditions.