How to air seal roof shed with rigid foam? This comprehensive guide unveils the secrets to transforming your shed into a cozy, energy-efficient haven. From choosing the perfect rigid foam to meticulously sealing every crack, we’ll equip you with the knowledge and techniques to create a robust, airtight barrier. Discover the myriad benefits of this crucial step, and elevate your shed’s performance to new heights.
Protecting your shed from the elements is paramount, and effective air sealing plays a pivotal role. Rigid foam insulation, with its superior properties, offers an ideal solution. This guide delves into the various types of rigid foam, their pros and cons, and the specific tools and materials required for the job. Prepare to embark on a step-by-step journey to a perfectly sealed shed roof!
Introduction to Air Sealing Shed Roofs with Rigid Foam
Air sealing shed roofs is a crucial step in improving energy efficiency and reducing drafts, ultimately extending the lifespan of the structure. Proper air sealing minimizes the infiltration of outside air, which can cause significant heat loss in winter and heat gain in summer. This leads to lower energy bills and a more comfortable interior environment.The application of rigid foam insulation effectively mitigates air infiltration through gaps and cracks in the roof structure, enhancing the overall thermal performance.
This approach significantly contributes to a more sustainable and cost-effective shed.
Types of Rigid Foam Insulation
Various types of rigid foam insulation are suitable for shed roofing applications. The selection often depends on factors like budget, desired insulation performance, and the specific needs of the shed.
- Extruded Polystyrene (XPS): XPS is a rigid foam known for its excellent resistance to moisture absorption. This characteristic makes it a good choice for roofing applications where moisture control is a priority. Its high compressive strength makes it suitable for applications where significant weight is anticipated. However, XPS is often more expensive than other options. It is commonly used in high-performance roofing systems where durability and moisture resistance are paramount.
For example, in coastal regions or sheds exposed to high humidity, XPS can be a worthwhile investment in long-term shed maintenance.
- Expanded Polystyrene (EPS): EPS is a less dense, less expensive foam. While it is not as resistant to moisture as XPS, it provides good insulation performance for its price point. Its lower compressive strength makes it less suitable for high-load applications. EPS is frequently used in applications where a balance of affordability and insulation is desired. It is commonly used for sheds in temperate climates where moisture infiltration is not a significant concern.
- Polyurethane Foam (PU): Polyurethane foam is known for its high insulation value and its ability to conform to complex shapes. This makes it an excellent choice for roofs with intricate designs or irregular surfaces. However, the installation process can be more complex and labor-intensive compared to other foam types. It is particularly useful for sheds with demanding thermal performance requirements, where significant temperature fluctuations are anticipated.
For example, a shed used for storing sensitive equipment or in areas with extreme temperatures.
Advantages and Disadvantages of Rigid Foam Types
- XPS: Advantages include high compressive strength, superior moisture resistance, and good thermal performance. Disadvantages include higher cost compared to EPS and potential environmental concerns associated with its production. Its relatively high cost often necessitates a long-term return on investment for the shed owner.
- EPS: Advantages include lower cost and good insulation properties. Disadvantages include lower moisture resistance, and potentially lower compressive strength than XPS. Its lower cost can be a significant factor for budget-conscious shed owners.
- PU: Advantages include excellent thermal performance, high conformability, and good adhesion. Disadvantages include a more complex installation process and potential environmental concerns associated with its production. Its use is most beneficial in sheds requiring very high insulation standards and where detailed installation is manageable.
Tools and Materials
Proper air sealing of shed roofs requires a range of tools and materials. Careful planning and selection are essential to ensure a successful and efficient installation process.
Tool/Material | Purpose | Estimated Cost (USD) | Notes |
---|---|---|---|
Rigid Foam Insulation | Provides the air sealing barrier | $50-$150+ (depending on type and quantity) | Consider the R-value for your climate. |
Roofing Adhesive | Bonds the foam to the roof | $20-$50 | Choose an adhesive suitable for the foam type. |
Utility Knife | For cutting foam to size | $5-$15 | Ensure a sharp blade for clean cuts. |
Measuring Tape | For accurate measurements | $5-$10 | Accurate measurements are critical. |
Caulk Gun | For applying sealant | $10-$25 | A quality caulk gun ensures proper application. |
Caulk/Sealant | Fills gaps and cracks | $10-$30+ (depending on type) | Use weather-resistant sealant for optimal results. |
Safety Glasses/Gloves | Personal Protective Equipment (PPE) | $5-$20 | Essential for safety during the project. |
Preparing the Shed Roof for Air Sealing
Proper preparation of the shed roof is crucial for effective air sealing with rigid foam insulation. A clean, dry, and sound roof surface ensures a strong, durable, and airtight seal, maximizing the insulation’s effectiveness and longevity. Neglecting these preparatory steps can lead to issues like premature failure of the foam, inadequate insulation performance, and even further damage to the roof structure.Thorough preparation minimizes the risk of leaks, air infiltration, and thermal bridging, leading to a more energy-efficient and comfortable shed.
This section details the steps involved in ensuring a suitable roof surface for the application of rigid foam insulation.
Surface Cleanliness and Dryness
Ensuring a clean and dry roof surface is paramount for optimal adhesion and longevity of the rigid foam insulation. Moisture, debris, and loose materials can hinder proper bonding and compromise the insulation’s performance. Removing these elements is critical for a successful air sealing project.
- Thoroughly inspect the roof for any signs of moisture. Look for areas with standing water, dripping, or damp patches. If moisture is present, address it before proceeding. Appropriate solutions include proper drainage, removing excess water, and utilizing a sealant or waterproof membrane.
- Remove all loose debris, such as leaves, twigs, dirt, and other foreign objects from the roof surface. This ensures a smooth and consistent surface for the foam application.
- Clean the roof surface with a suitable detergent and water solution. A stiff-bristled brush can be effective for removing stubborn debris. This will ensure a clean surface to improve adhesion. Use a high-pressure water washer to clean off large areas efficiently, but be mindful of possible damage to the roofing materials.
Removing Existing Insulation and Debris
The presence of existing insulation or debris on the roof can impede the proper installation of rigid foam. Removing these materials ensures a clean surface for the new insulation.
- Carefully remove any existing insulation materials from the roof. If the insulation is firmly adhered, use specialized tools or techniques to avoid damaging the roof. Be careful not to damage the roof sheathing during removal. If the insulation is loose, simply remove it by hand or using a scraper.
- Remove all loose materials, including deteriorated shingles, broken flashing, or other loose debris. This ensures that the new foam is in direct contact with a solid and stable surface. Any loose material can interfere with the insulation’s performance.
Roof Inspection for Leaks and Damages
Identifying and addressing existing leaks or damages is crucial before applying new insulation.
- Inspect the roof for any signs of leaks or damage. Check for holes, cracks, or missing shingles. Use a flashlight to inspect hard-to-reach areas.
- Look for areas where water may be accumulating or pooling. These areas are potential sources of leaks.
- If leaks or damage are found, address them before installing the rigid foam. Repairing these issues prevents water damage and ensures the longevity of the insulation.
Step-by-Step Roof Preparation Procedure
The following table Artikels a step-by-step procedure for preparing the shed roof for rigid foam installation.
Step | Description | Image 1 (Roof Inspection) | Image 2 (Debris Removal) | Image 3 (Surface Cleaning) | Image 4 (Damage Repair) |
---|---|---|---|---|---|
1 | Thorough visual inspection of the roof for any signs of damage, leaks, or moisture issues. | (Image of a person inspecting the roof with a flashlight) | (Image of roof with debris) | (Image of a roof with a detergent and water solution) | (Image of a repair on a damaged shingle) |
2 | Removal of loose debris, such as leaves, twigs, and dirt, using appropriate tools like a broom or soft brush. | (Image of a person removing debris) | (Image of the roof after debris removal) | (Image of the roof surface after cleaning) | (Image of the roof showing repair completion) |
3 | Cleaning the roof surface with a suitable detergent and water solution to ensure a clean surface for foam adhesion. | (Image of the roof before cleaning) | (Image of the cleaning process) | (Image of the cleaned roof) | (Image of a professional checking the repaired roof) |
4 | Repairing any identified leaks, holes, or damages to prevent water penetration. | (Image of a roof with a leak) | (Image of the damaged area) | (Image of a repair process) | (Image of a fully repaired roof) |
Installing Rigid Foam for Air Sealing: How To Air Seal Roof Shed With Rigid Foam
Proper installation of rigid foam insulation is crucial for achieving effective air sealing on shed roofs. Incorrect installation can lead to gaps and voids, negating the intended benefits of the air sealing process. Careful adherence to the installation techniques Artikeld below ensures a tight seal and optimal energy efficiency.
Adhesive Application
Adhesive application is a key aspect of foam installation. Appropriate adhesive selection is vital for long-term adhesion and structural integrity. Contact adhesives, known for their rapid bonding, are often used. However, the choice depends on the specific foam type, roof sheathing material, and climate conditions. Manufacturers’ recommendations should be consulted for optimal performance.
- Thorough surface preparation is essential before adhesive application. Clean the roof sheathing thoroughly to remove any dust, debris, or loose material. Ensure the surface is dry and free of any contaminants that could impede bonding.
- Adhesive application should follow the manufacturer’s instructions meticulously. Apply the adhesive evenly to the back of the foam panel, ensuring complete coverage. Over-application can lead to drips and potential issues with proper installation. Conversely, insufficient adhesive may result in inadequate adhesion, leading to gaps.
- Allow the adhesive to cure completely according to the manufacturer’s specifications. This step is critical for achieving maximum bonding strength. Improper curing times can lead to premature failure of the adhesive bond, and thus, the foam panel.
Mechanical Fastening, How to air seal roof shed with rigid foam
Mechanical fasteners, such as nails or screws, can supplement or replace adhesive in some instances. They provide additional structural support, particularly in areas with high wind loads or where significant movement might occur.
- Using the appropriate fastener type is paramount. The fastener should be compatible with both the foam panel and the roof sheathing material. Nails are often used for softer materials, while screws are suitable for stronger sheathing. Oversized fasteners can damage the sheathing, while undersized ones may not provide sufficient holding power.
- Properly positioning the fasteners is critical. Follow the manufacturer’s instructions for spacing and depth to avoid damaging the foam or sheathing. Overlapping or misaligned fasteners can compromise the seal. Avoid placing fasteners directly over critical joints in the foam to prevent potential failure.
- Fasteners should be driven in straight, without bending or twisting the foam panel. Careful handling prevents warping and damage, thus maintaining a smooth surface. Over-tightening can deform the panel, creating gaps.
Foam Thickness and Coverage
Precise foam thickness and complete coverage are essential for effective air sealing. Inadequate thickness can result in insufficient insulation and air barrier performance.
- Consult manufacturer recommendations for the ideal foam thickness required for the desired R-value and the shed’s climate zone. Different foam types have varying R-values per inch of thickness.
- Ensure that the foam panels cover the entire roof area, without any gaps or overlaps. Carefully trim or cut the foam to fit the roof’s contours. Seal any seams or joints between panels with appropriate sealant to maintain a continuous air barrier.
Foam Panel Sizes and Suitability
The appropriate foam panel size significantly impacts installation efficiency and cost-effectiveness.
Panel Size (ft²) | Suitable Roof Area | Pros | Cons |
---|---|---|---|
2′ x 4′ | Small to medium-sized areas, easy to handle, and precise cutting | Easy to work with, cost-effective for smaller sheds | May require more panels for larger areas |
4′ x 8′ | Medium to large-sized areas, suitable for most shed roofs | Efficient for larger areas, reduces installation time | Can be cumbersome to handle, potentially higher cost |
6′ x 10′ | Large-sized areas, ideal for extensive shed roofs | Very efficient for very large roofs, minimized seams | Difficult to handle, high cost for larger sheds |
Sealing Gaps and Cracks
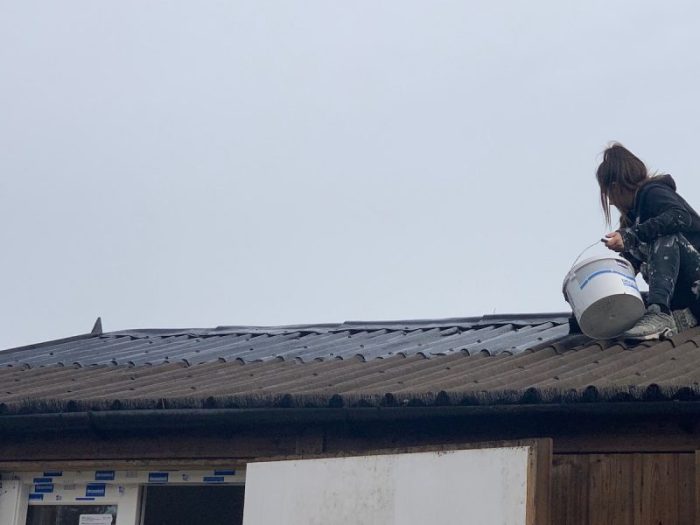
Proper air sealing of a shed roof is not just about insulating the structure; it’s about creating a barrier against drafts, moisture, and pests. Neglecting gaps and cracks in the roof perimeter can significantly reduce the effectiveness of insulation and compromise the overall thermal performance of the shed. This crucial step prevents heat loss in winter and heat gain in summer, ultimately leading to energy savings and a more comfortable indoor environment.Comprehensive air sealing extends beyond the insulation itself.
Thorough sealing of all gaps and cracks in the roof’s perimeter, including those around flashing, vents, and penetrations, is vital to achieve the desired level of insulation performance. This attention to detail minimizes air infiltration, improving the shed’s overall energy efficiency and reducing the potential for moisture damage.
Identifying Potential Gaps and Cracks
Thorough inspection is paramount for effective air sealing. Begin by visually inspecting the entire roof perimeter, paying particular attention to areas where materials meet (e.g., roof sheathing, fascia boards, and vents). Using a flashlight or a small mirror, check hard-to-reach areas for cracks or gaps. A blower door test can be a helpful tool for identifying significant air leaks.
These tests use a fan to force air through the structure and measure the rate of leakage. This method can reveal hidden air leaks that might not be immediately apparent during a visual inspection.
Methods for Sealing Gaps and Cracks
Proper sealing methods depend on the size and nature of the gap or crack. A variety of materials can be used for sealing, each with specific properties and applications.
- Caulk: Caulk is a versatile sealant, effective for sealing small gaps and cracks. It comes in various forms, including acrylic, polyurethane, and silicone. Acrylic caulk is commonly used for interior applications due to its flexibility and water resistance. Polyurethane caulk is often favored for exterior use due to its superior weather resistance. Silicone caulk is a highly versatile choice, providing excellent adhesion to many surfaces and a wide range of temperatures.
Choose the type of caulk that best suits the specific application and environmental conditions.
- Sealant: Sealants are often used for larger gaps or for sealing around penetrations. Different sealants are available with varying properties, like flexibility, adhesion, and resistance to moisture and UV exposure. Selecting the appropriate sealant is crucial for long-term effectiveness. Some common sealants include expanding foam, elastomeric sealants, and butyl rubber tape.
- Spray Foam: Spray foam insulation is highly effective for filling large gaps and creating a continuous airtight barrier. It expands to fill voids completely, providing an excellent air barrier. Spray foam is often used in conjunction with other sealing methods, providing a robust and comprehensive solution. This method is particularly beneficial for areas with complex geometries or significant gaps that require a tight seal.
Recommended Sealants and Applications
A variety of sealants are suitable for air sealing shed roofs. The choice depends on the specific application and the environmental conditions.
- Acrylic caulk: Suitable for interior and exterior use, particularly for small gaps and cracks.
- Polyurethane caulk: Excellent for exterior applications, especially those requiring high weather resistance.
- Silicone sealant: Versatile and suitable for both interior and exterior use. Provides excellent adhesion and flexibility.
- Expanding foam sealant: Ideal for filling larger gaps and cracks, especially around penetrations.
Comparison of Sealing Methods
The table below provides a comparison of different sealing methods based on their effectiveness, cost, and application.
Sealing Method | Effectiveness | Cost | Application |
---|---|---|---|
Caulk (Acrylic) | Good for small gaps | Low | Interior and exterior |
Sealant (Polyurethane) | Good for larger gaps | Medium | Exterior |
Spray Foam | Excellent for large gaps and complex geometries | Medium-High | Complex gaps, penetrations |
Finishing Touches and Considerations
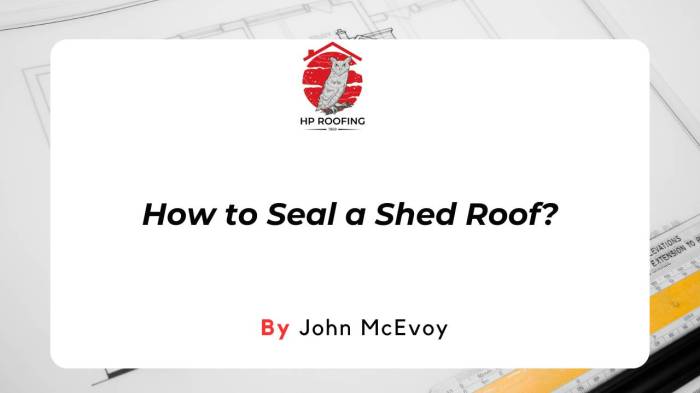
Completing the air sealing process for a shed roof with rigid foam requires meticulous attention to detail, ensuring a lasting and effective seal. Proper finishing touches, ventilation strategies, and thorough inspection are crucial for maintaining the structural integrity and thermal performance of the shed. These final steps will ensure the shed is well-insulated and energy-efficient, maximizing its lifespan and utility.
Finalizing the Air Seal
Thorough application of sealant to all gaps and cracks is essential. This step involves carefully inspecting all previously sealed areas and identifying any overlooked gaps or imperfections. Applying a high-quality sealant, such as a polyurethane or acrylic sealant, to these areas is critical to achieving an airtight seal. The sealant should be applied evenly and smoothly to completely fill the gaps, creating a barrier to air infiltration.
Using a sealant gun and appropriate tools, such as caulking tools or a sealant applicator, will facilitate efficient application. Ensuring the sealant is fully cured according to the manufacturer’s instructions is vital for long-term effectiveness.
Ventilation Strategies
Proper ventilation is crucial for preventing moisture buildup and promoting healthy indoor air quality within the shed. This includes establishing a balance between maintaining the air seal and allowing sufficient airflow to prevent condensation. The ventilation strategy should be tailored to the specific shed design and the climate conditions. Sheds with multiple roof vents and ridge vents can be used to create a controlled airflow pattern.
Ensure the shed roof’s ventilation system allows for adequate air circulation, preventing moisture build-up. Consider using ridge vents and soffit vents to promote airflow. Maintaining proper ventilation will help prevent mold and mildew growth and ensure the shed’s longevity.
Inspection and Airtightness Testing
Thorough inspection of the finished work is essential to identify any remaining gaps or leaks. This involves visually inspecting all sealed areas for any signs of incomplete sealing or gaps. Use a flashlight to inspect hard-to-reach areas. This step is vital to ensuring a complete and effective air seal. The effectiveness of the air sealing process can be validated through air pressure testing.
Using a blower door or similar device, carefully monitor air pressure differences between the interior and exterior of the shed. A consistent and minimal pressure difference indicates an airtight seal.
Best Practices and Safety Precautions
The following table summarizes best practices and safety precautions for air sealing a shed roof with rigid foam.
Step | Best Practice | Safety Precautions | Tools and Materials |
---|---|---|---|
Applying Sealant | Apply sealant evenly and completely fill gaps. | Wear appropriate safety glasses and gloves. Use caution when handling sealant. | Sealant, sealant gun, caulking tools, gloves, safety glasses |
Ventilation | Ensure adequate ventilation to prevent moisture build-up. | Use appropriate ventilation systems and techniques. | Vents, fans, ventilation ducts |
Inspection | Visually inspect all sealed areas for gaps. | Use a flashlight to inspect hard-to-reach areas. | Flashlight |
Airtightness Testing | Conduct air pressure tests to evaluate the seal. | Ensure proper ventilation during testing. | Blower door, pressure gauge |
Troubleshooting Common Issues
Effective air sealing of shed roofs with rigid foam requires careful attention to detail and proactive problem-solving. Potential issues, ranging from installation difficulties to inadequate sealing, can impact the final performance of the insulation. This section details common problems and their solutions, promoting successful and durable air sealing.
Foam Installation Issues
Proper foam installation is crucial for a successful air seal. Improper installation methods can lead to gaps, voids, and inadequate insulation performance. Adherence to manufacturer guidelines and using appropriate tools and techniques are paramount. For instance, insufficient foam thickness can compromise the insulation’s ability to effectively block air infiltration. Similarly, uneven application can create weak points that allow air to leak through.
Sealing Gaps and Cracks
Gaps and cracks around penetrations, such as vents, pipes, and flashing, are common sources of air leakage. These openings must be meticulously sealed using appropriate sealant materials. A variety of sealants, such as spray foam, caulk, or weatherstripping, can be employed depending on the specific gap or crack. Incorrect sealant selection can lead to premature failure, as some sealants may not be suitable for the specific environment or material.
For example, using a sealant incompatible with the roof’s material can result in deterioration or cracking.
Ventilation Concerns
Ventilation plays a critical role in maintaining a healthy shed environment. Inadequate ventilation can lead to moisture buildup and potential mold growth. Conversely, excessive ventilation can compromise the insulation’s effectiveness. A balanced approach to ventilation, taking into account the shed’s location and climate, is vital. Properly designed and installed vents will ensure adequate airflow while maintaining the insulation’s integrity.
Common Mistakes and Solutions
- Incorrect Foam Thickness: Using insufficient foam thickness compromises insulation performance. Ensure the foam thickness meets the requirements for the shed’s climate and insulation standards. Consult the manufacturer’s guidelines for proper thickness.
- Improper Foam Adhesion: Foam that does not adhere properly to the roof surface will create gaps, allowing air leakage. Ensure the roof surface is clean, dry, and primed before foam application. Using the correct adhesive and applying it according to the manufacturer’s instructions is crucial.
- Inadequate Sealing of Penetrations: Gaps around pipes, vents, and other penetrations are significant sources of air leakage. Thoroughly seal all penetrations using appropriate sealant materials and techniques.
- Neglecting Vapor Barriers: Neglecting vapor barriers can result in moisture buildup within the insulation. A vapor barrier is essential for preventing moisture from entering and compromising the foam’s performance. This is especially critical in humid climates.
Preventing Issues
Thorough planning and preparation are key to avoiding potential problems. Accurate measurements, careful material selection, and adherence to installation guidelines are critical. Checking for any pre-existing structural issues and addressing them before beginning the insulation process is important to prevent future complications.
Frequently Asked Questions (FAQs)
- What type of sealant is best for air sealing a shed roof? The best sealant depends on the specific material and location. Consult with a professional or refer to the manufacturer’s recommendations for the best sealant option.
- How often should I inspect the air sealing? Regular inspections are crucial for identifying and addressing potential problems. Visual inspections and thermal imaging can be used to detect air leaks.
- Can I use different types of rigid foam for the same shed? Using different types of rigid foam might lead to inconsistencies in the insulation performance. It’s best to use the same type of foam throughout the entire project for consistent results.
- How can I ensure proper ventilation after air sealing? Proper ventilation is essential for moisture control. Strategically place vents to ensure adequate airflow and prevent moisture buildup. Consider the shed’s climate and orientation.
End of Discussion
By meticulously following the steps Artikeld in this guide, you’ll be well-equipped to air seal your shed roof using rigid foam. Remember, a thorough approach to preparation, installation, and sealing is key to achieving an airtight and energy-efficient structure. This comprehensive guide provides the essential knowledge and techniques to complete the project successfully, transforming your shed into a comfortable and durable space.
So, embrace the challenge, and watch your shed transform!
FAQ Summary
What are the most common types of rigid foam used for shed roof air sealing?
Extruded polystyrene (XPS) and Polyurethane foam are popular choices due to their durability and insulating properties. Expanded polystyrene (EPS) is also a viable option, though it might be less robust.
How often should I inspect my shed roof for leaks after air sealing?
Regular inspections, especially after periods of heavy rain or snow, are crucial. Check for any signs of water intrusion around the foam installation areas.
What are some common mistakes to avoid when installing rigid foam panels?
Improperly adhering the foam panels, insufficient foam thickness, and neglecting to seal gaps around the perimeter are frequent errors. Ensure proper adhesion and adequate coverage for a strong seal.
What if I find a leak after completing the air sealing process?
If you discover a leak, thoroughly inspect the area for gaps or imperfections. Recheck the foam installation and sealing process, and apply additional sealant if necessary. If the issue persists, consult a professional.